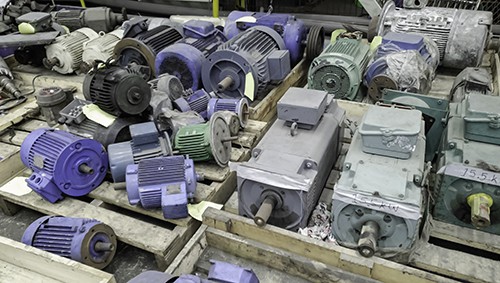
An example of less than ideal electric motor storage.
Electric motor failures happen. That’s why, in an effort to minimize downtime, it’s common practice for manufacturing companies to store spare motors that can be easily swapped out for a failed motor. However, having stored equipment is only beneficial if it’s kept “operation-ready” – and this requires proper management and regular service to ensure reliability.
Here are five things to consider to better ensure your capital investment is protected:
Where will motors be stored?
Ideally, electric motors should be stored indoors in a clean, dry, climate-controlled environment. If outdoor storage is the only option, motors should be palletized and covered with a loose, waterproof cover that allows for adequate air circulation and minimal condensation.
How long will motors be stored?
We advise referring to storage procedure instructions for your specific brand of electric motor. The following are general guidelines:
- Short Term (Less than 1 month) For motors that will be in storage for less than a month, maintaining a temperature of 10-20 degrees F above room temperature is ideal to providing winding temperature protection. If the temperature is difficult to control, use space heaters or try “trickle heating” one phase of the winding on low voltage.
- Mid Term (From 1 to 12 months) For storage from 1 to 12 months, follow the procedure stated above for short-term storage along with more thorough monthly inspections, recording the stator winding insulation resistance level.
- Long Term (beyond 12 months) For motors that need to be stored longer than 12 months, follow the above procedures. To prevent damage from contamination gases present in the storage area, a yearly oil change and re-lubrication of bearings is recommended.
Will stored motors be affected by ambient vibration?
Sometimes, storage locations will be near sources of ambient vibration such as rail lines, heavy construction equipment, production floors, and forklift traffic. Long-term exposure to ambient vibration can cause internal bearings to vibrate, resulting in a defect known as false brinelling. False brinelling is a type of bearing damage caused by fretting (with or without corrosion) that causes hollow spots that look similar to Brinell dents in the bearing’s outer race. While this may not seem significant, it will show up as noise and appear in the vibration signature once the spare motor is put in service.
How will motors be stored?
When possible, electric motors should be stored vertically to lessen the excess weight from the rotor and shaft assembly on the bearings. When vertical storage isn’t possible, rotating the shaft 10-15 revolutions on a weekly basis (quarterly at a minimum) will prevent wear from being centralized to individual locations on the bearing components. Shafts of larger motors should be turned more often.
Will stored motors be protected from pests?
During storage (particularly outdoor storage), motors can be exposed to pests such as rodents, insects, and birds. If these enter the motor, they can damage winding insulation and block ventilation and drain openings. Precautions can be taken to reduce this risk such as:
- Storing motors in original containers
- Placing steel wool in drain holes or openings
- Placing mothballs around the perimeter of the storage area
- Placing scented dryer sheets in crevices of motors or in the container
The cost of interrupted production can have significant implications for your company’s bottom line. When a motor is removed from storage, it needs to be in good operating condition and “ready for service.” Having a plan in place for conducting a few relatively simple maintenance steps during storage is critical to ensuring that your spare motor operates properly when it’s installed. We can help – contact us.