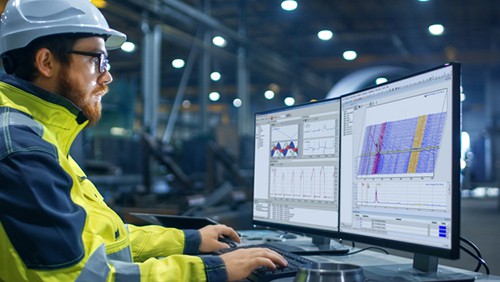
(Photo courtesy of iba)
Data collection on rotating equipment is a key component to understanding the condition of your industrial equipment. Accuracy and consistency are crucial because if your data isn’t accurate, its subsequent analysis won’t be either. Additionally, early warning signs indicating developing problems could be missed if data acquisition isn’t accomplished in a timely manner. These issues can result in costly downtime and lost productivity.
Manufacturing companies who want to remain competitive and profitable in today’s uncertain global economy have realized the pivotal role that data and analytics play in improving operational efficiency and effectiveness. Integrating process and condition monitoring while harnessing the resulting data is a necessary first step in developing a strategic approach to decrease downtime and increase productivity.
The right tools and procedures used for integrating process condition monitoring are absolutely critical. If applied correctly they can accurately identify influences in production machinery and the associated process control systems, which allows the evaluation of effects on the produced product where quality ultimately matters.
One such tool that we’ve added to our advanced testing arsenal is the iba Multi-Channel Portable Process Data Acquisition System.
Simply put, IVC took iba’s cutting edge process data acquisition system and made it portable to provide our customers with easily accessible advanced technology with which to better monitor their machines.
The advantages of this new portable system include the fact that:
- It features a 32-channel capacity for simultaneous data recording
- It can be easily deployed for places that aren’t easily accessible such as certain types of cranes, wind turbines, and off-shore oil rigs
- An imbedded computer allows the system to be preconfigured and shipped to a technician for rapid deployment
- Data collection begins as soon as the unit is powered up
- The four input modules inside can be changed out to meet specific criteria (i.e. digital, analog)
We’d love to show you the “magic” inside the box but it’s…
Real-life example of how integrated process condition monitoring helps solve Chatter
Both Rolling Mill and Roll Grinder chatter are quality issues that no manufacturer can afford. They result in lost production, increased conversion costs, and a loss of reputation and market share. Typical vibration analysis techniques fall short because they cannot characterize everything that occurs during the course of a coil or a grind with a single snapshot of data. Integrated process condition monitoring provides a decisive solution to a complicated situation.
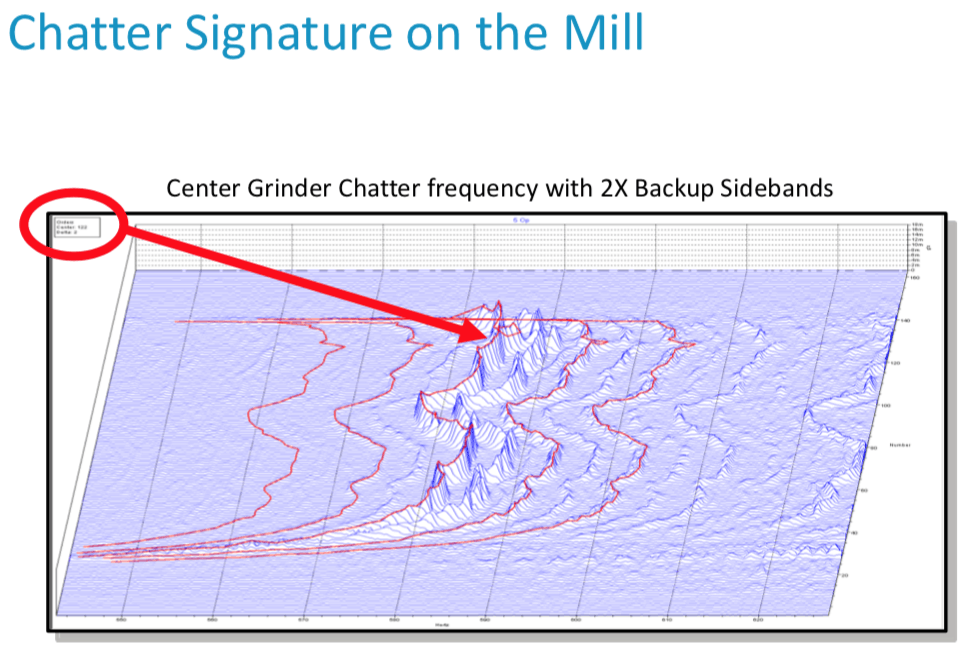
Chatter Signature on the Mill – Integrating Process and Condition Monitoring
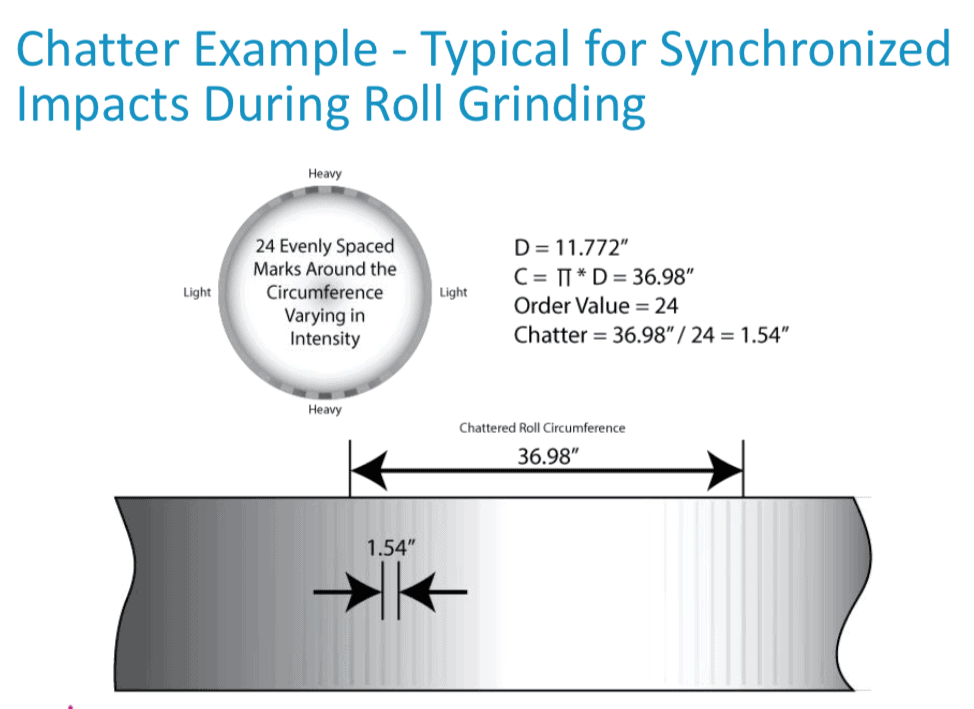
Chatter Example Integrating Process and Condition Monitoring – Typical for Synchronized Impacts During Roll Grinding
Customizing is key to avoid getting in too deep, too quickly
The pandemic has hit everyone hard – especially the manufacturing industry. Now more than ever, companies want to avoid biting off more than they can chew when it comes to machine maintenance.
The robust and flexible nature of iba systems can help you to do just that as they can be easily customized to meet the needs of the application, regardless of the complexity. You only configure the interfaces and signals needed to capture your process. When maintenance budgets are tight (as many are now), this allows companies to start small and add additional interfaces, signals, data stores, etc. as requirements grow.
At IVC, we’re always striving to stay “ahead of the pack” by continually moving ahead and improving the tools and techniques we use to keep your equipment running at optimum efficiency. We focus on analyzing and improving your process, production, and bottom line.
We’re ready to help you tackle your toughest production and quality problems. Contact us to see how we can work together.