Can 2020 just be over already?
For the manufacturing industry, the COVID-19 pandemic has accelerated the transition to automation and digitization, as factories try to remain operational with fewer employees on-site to manage it, and with social distancing guidelines in place.
Adding to the difficulty is the industry’s ongoing struggle to find enough candidates with the right skills and talents to fill open positions.
In fact, according to the Manufacturing Institute’s 2020 Training Survey, “manufacturers have consistently cited the inability to attract and retain talent as their top business concern.” Also, among the survey’s findings:
- Nearly 70% of manufacturers are addressing the workforce crisis by creating and expanding internal training programs for their workforce.
- Three-quarters of respondents said that upskilling workers helped to improve employee productivity.
- The manufacturing sector spent at least $26.2 billion in 2019 on internal and external training programs for new and existing manufacturing employees.
“For the best return on your money, pour your purse into your head.” – Benjamin Franklin
We see it all too often. In an effort to stay competitive, companies factor in the costs for updating their machine maintenance technologies (e.g. new wireless sensors, a new CMMS system) but they forget about another valuable asset that also needs regular “updating”: their employees.
Upskilling, reskilling, and keeping the saw sharp
You can’t read an article on manufacturing these days without hearing “buzzwords” like upskilling (employees learn new skills to help in their current roles) and reskilling (employees learn skills needed for an entirely new role.)
While these concepts are relevant in almost any industry today, upskilling is particularly important to the manufacturing industry as technological advancements show no signs of slowing down. It’s amazing how quickly one can get rusty on technologies that aren’t utilized every day but are still a necessary component of the job’s core expectations. That’s why providing employees with regular refresher training to help keep the saw sharp is crucial.
What makes IVC training programs different
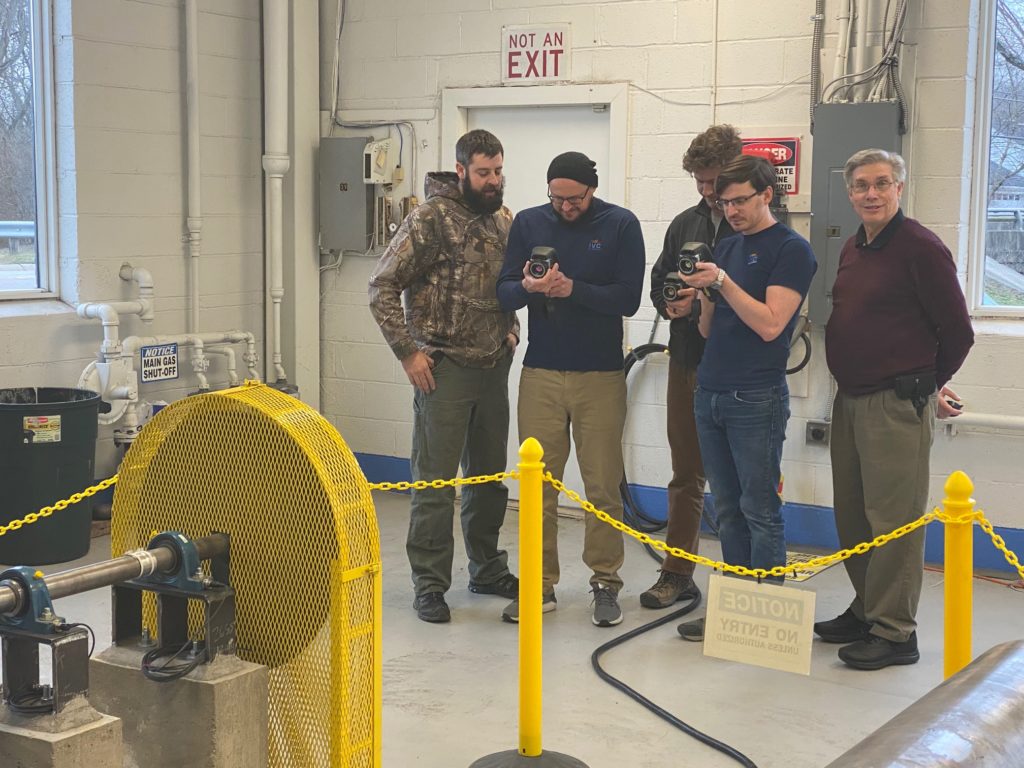
IR training in IVC’s on-site lab
The sad (and frankly scary) thing is that in today’s always-connected world where practically everything is but a finger stroke away…anyone can get “certified” in just about anything they want. But that doesn’t mean that they are at all qualified for the work they claim to be able to do.
We were dismayed after sending our own employees to various training programs, only to have them return, proudly and officially certified, yet still unable to actually perform the tasks they’d just passed a test on.
That’s when IVC decided to create our own training programs as well as an on-site training lab with real machinery so that we could provide genuine hands-on, practical training on equipment that attendees will likely encounter in the field. In addition, the classroom portion of our training programs is taught by experienced field analysts, teaching concepts that extend beyond what is in the training manual.
We also understand that each company’s training needs are unique. That’s why our programs are tailored to meet the specific needs of each company.
Start the new year off strong
So, as you plan your budget for 2021, don’t forget to factor in training opportunities for your employees. Check out our 2021 training schedule and contact us to find out more about developing a specialized training program for your valued crew.