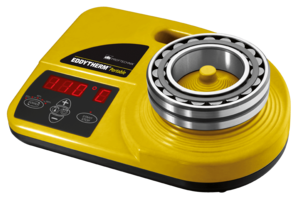
PRÜFTECHNIK’s EDDYTHERM® Portable and compact induction heater with a magnetic temperature probe up to 180°C
In theory, roller bearings can outlive the machinery in which they perform. In reality, however, bearings fail prematurely for a myriad of reasons such as lubrication failure, contamination, and misalignment. As analysts, one critical reason we encounter frequently is improper mounting.
In fact, an estimated 16 percent of all premature bearing failures can be attributed to poor fitting. This is often due to using brute force during installation and lacking the knowledge of correct fitting tools.
The main objective when mounting a bearing is to apply the minimum amount of force with maximum control. Employing best practices can go a long way in avoiding future problems, thereby extending its service life.
But what are these “best practices”?
Bearing Mounting: From Cold to Hot
The primary methods for mounting a bearing are referenced as “hot” or “cold” based on their enabling technologies. Cold mounting is typically recommended for small- and medium-sized bearings (having outside diameters up to 4″). In contrast, mounting methods that involve heat are recommended for larger bearings.
Specific tools have been designed for each particular method.
Cold Mounting
Due to the damage that can occur, the practice of using a standard hammer and pipe for cold mounting has long since been discredited. This method of mounting can cause debris to enter the bearing. When not done properly, it can also cause the pipe to slip and impact the internal structures of the bearing.
Best practice: Fitting tools ensure that proper force is applied to both bearing rings. In addition, rolling elements are isolated from impact force, providing a more reliable installation while limiting the risk of damage.
Hot Mounting
Hot mounting involves pre-heating the bearing. The heat allows for a bearing’s expansion resulting in an easier installation, while still maintaining specified interference fit. However, the method of heat application can make a substantial difference.
For example, pre-heating bearings via hot oil baths raises the likelihood of contamination and premature bearing failure and flashing. Other methods such as hot plates, ovens or exposure to an open flame can also be potentially dangerous.
Best practice: Induction heating allows a high degree of control, efficiency, and safety. Induction heaters, including portable versions like PRÜFTECHNIK’s EDDYTHERM Portable (for bearings up to 10 kg), are equipped with advanced technologies that promote consistent performance, ease of use and most importantly, safety for the operating personnel.
An important thing to keep in mind: Induction heaters produce an electric current, which magnetizes the bearing. Demagnetization is essential to prevent the attraction of metal particles and potential contamination leading to premature bearing failure. To address this, manufacturers like PRÜFTECHNIK have designed induction heaters that automatically demagnetize the bearing at the end of the heating cycle. Both the EDDYTHERM 4x (for heavy workpieces up to 300 kg) and the EDDYTHERM 2x (for small and midsize bearings) both have automatic demagnetization built into their design.
At IVC, we understand the vital role that bearings play in rotating machinery and have helped numerous clients get to the root cause of premature bearing failure. Contact us to see how we can help you extend the life of your bearings.