This is Part 2 in our 4-part series on maintenance programs and benchmarking. If you missed Part 1, read it now. This week, we move on to evaluating equipment maintenance programs to determine the best course of action. It’s important to consider the pros and cons of the different styles of maintenance plans, including reactive maintenance, preventive maintenance (sometimes also called preventative), and predictive maintenance options.
Which program is the most cost effective?
Corrective/Reactive Maintenance (CM)
Otherwise known as the “fix it when it breaks” method of maintenance, it has a major drawback: the cost to repair or replace equipment that has been run to failure is usually significantly higher than if issues were detected and fixed earlier on, not to mention the cost of lost production time while the machine is out of service.
Preventive Maintenance (PM)
A preventive maintenance (PM) plan operates under the assumption that with regularly scheduled service, whether it’s needed or not, equipment will remain relatively reliable until such time as it naturally begins to wear out. Determining when a piece of equipment will enter the “wearing out” phase has traditionally relied on general estimates and averages instead of actual stats on the condition of specific equipment. This often results in costly and completely unnecessary, maintenance taking place before there is any actual problem or after potentially catastrophic damage has begun.
Predictive Maintenance (PdM)
Top quartile performers implement best practices in machine maintenance by following a predictive maintenance program. Predictive maintenance involves machine-specific monitoring of its efficiency and wear. These predictions are based on data collected from expert observation and tools such as vibration analysis, thermal imaging, ultrasonic analysis, operation availability, oil analysis and non-destructive testing. The model processes the information through predictive algorithms, discovers trends and identifies when equipment will need to be repaired or retired.
Teams perform predictive maintenance activities while the machines are running their normal production modes. As a result, an asset’s longevity is increased, maintenance costs and unnecessary inventory are reduced, and a company’s overall downtime is significantly decreased.
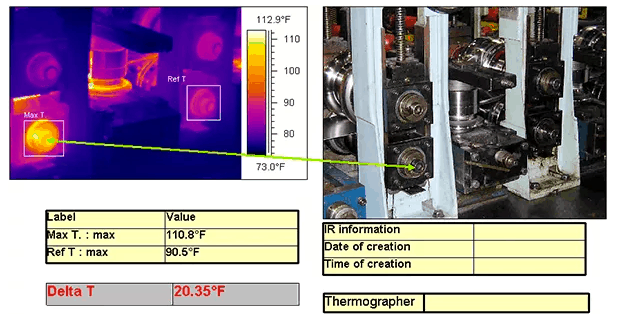
This graphic is an example of how IVC’s Infrared Thermography revealed a thermal issue before it became a catastrophic problem. Had the issue continued unresolved, it would have required machine shutdown and expensive repairs.
Inventory Overload?
In addition to the maintenance program you choose, the other important piece of the benchmarking puzzle is your company’s inventory. If you think carrying unnecessary inventory is only a warehouse space problem, you’re missing out on cost savings opportunities. Contact us to learn how IVC Technologies can help ensure you’re not carrying more inventory than necessary.
Coming next week…how too much inventory could be the thing standing between you and a healthy bottom line.