When looking at any manufacturing industry, there’s a system of equipment and processes. There are raw materials, a conversion process, and then finished goods and products.
Questions to Ask Yourself
Can you control what your raw material costs are?
Can you control what the market share of your finished product is?
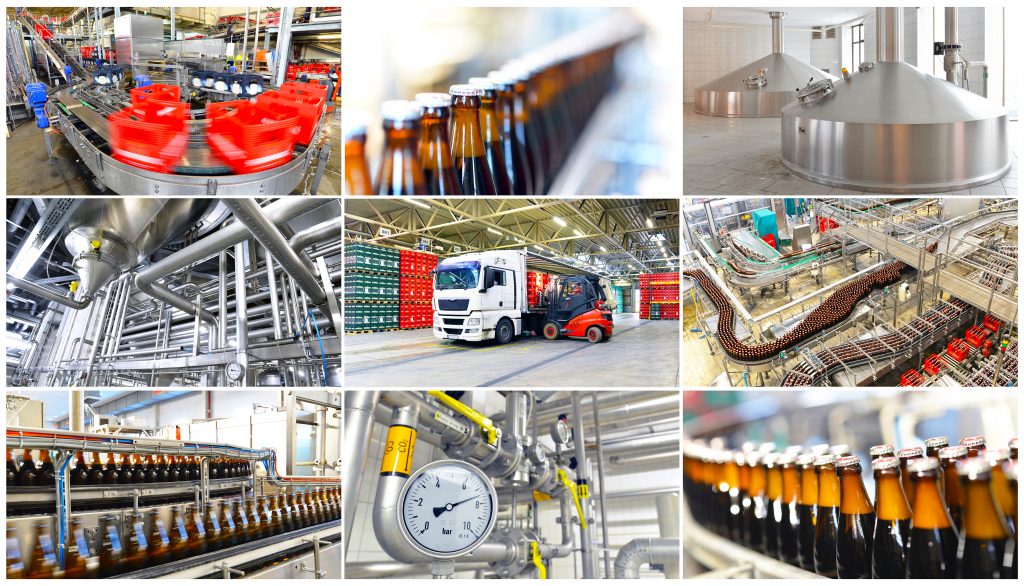
Elements of beverage production.
The answer to the two questions above is no. You typically have little or no control over the cost of raw materials or the market share of your finished product at the production level.
What Can You Control?
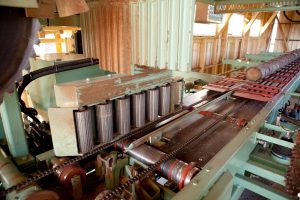
A log ready to be cut in a mill.
You can control the cost of conversion by becoming more efficient in your ability to convert the raw materials you have into finished products. The more efficiency that you can put into this process, the more profit the company makes.
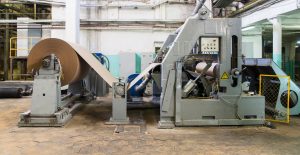
Roll of paper and paper-making machine.
Why is Profit Important?
Profits in the big picture, at a minimum, keep the doors open as well as being the source for bonuses and raises. If your plant runs inefficiently while operating, it will narrow greatly the profits possible to distribute as profit-share or bonuses, etc.
Think of it like this, if a plant uses everything or nearly everything it makes in profits to maintain the processes to get raw materials converted to products out the door into the market, then it’s just a straight bust. This kind of waste in efficiency is typically a process issue created by a gap in training or a general misunderstanding of technologies that exist that will create efficiencies.
Predictive maintenance (PdM) technology application is one way to gain efficiency in production through condition monitoring (CM) and the application of condition-based maintenance (CBM).
This will positively impact the health of critical assets to enable optimal health and consistent production of quality products the first time out. Simply put, controlling manufacturing inefficiencies reduces production costs and improves profits.
In fact, I bet if you think about it right now, there are probably processes at your facility today that run in the negative numbers that lose your company money. Knowing which technologies apply to your equipment in finding faults and impending failures will greatly improve your ability to plan and execute necessary maintenance at a greatly reduced overall cost to your organization.
In the Trenches
Plant maintenance personnel are the ones that turn the wrenches, and they’re the ones that can make sure things operate correctly and efficiently. This is why training and refresher training on PdM technologies, such as Vibration Analysis, Infrared Thermography, Oil Analysis, Ultrasonics, and even basic Visual Inspection is so important and one of the simplest things that you can immediately deploy to address controlling costs proactively.
What to Measure?
Measurement is true to the heart of any improvement process. You’ve surely heard some variance of:
“What gets measured gets done.” – W. Edwards Deming
“If it cannot be measured, it cannot be improved.” – Peter Drucker
It is my belief that:
“If you don’t measure it, you cannot manage it. It manages you, and it usually does it at three a.m.”
What is the Impact of Inefficiency?
Lost productivity, that time when you can’t make any product, all adds up into what it costs to convert. When a process breaks down, you’re going to put in overtime, and find yourself expediting parts, and all of these maintenance costs will add up quickly! Unplanned outages and overtime just cost more. Expediting parts costs more. Oh, and that bonus you were hoping for just got spent.
By understanding the available tools in your toolbox, and how to utilize them, you could positively impact the operations you are directly responsible for, improving efficiency and bottom-line revenue identified as profit.