As anyone in the field of condition based monitoring can tell you, there are any number of issues that can cause a machine to vibrate excessively such as unbalance, bearing failure, and cracked welds to name a few.
Often times, however, the aforementioned conditions are not the cause of the excessive vibration problem, but rather, the symptoms of a bigger issue: resonance.
What is resonance and why is it so difficult to diagnose?
Simply put, resonance is the amplification or intensification of vibration due to a natural frequency. Another way to think about it is to consider resonance as a mechanical amplifier.
Every machine, physical structure, and even animals have natural frequencies that can be excited. Resonant vibration occurs when the natural frequency of a machine is at or close to a forcing frequency such as rotor speed. When present, this condition can amplify small vibratory forces from machine operation significantly enough to cause equipment failure and plant downtime, quality problems, etc.
Resonance is particularly common in variable speed equipment and/or equipment that has recently undergone a running speed change.
What makes resonance so difficult to diagnose is the fact that the condition may only occur at certain points during the day – typically when demand requires that the machine run at a specific, problematic speed. By contrast, when the natural frequency is not excited (e.g. amplified) the machine may function completely normally.
We often hear customers say…
“But we do regular route-based maintenance so we should be able to detect resonance, right?”
Unfortunately, not necessarily. This is because detection may depend on specific operating conditions at the time of data collection. This means there’s an excellent chance that the natural frequency of the machine in question isn’t being excited. The best way to detect and understand the effects of resonance is to continually monitor a machine over a period of time.
Techniques used to identify and/or confirm resonance
There are many techniques available to identify and/or confirm a high vibration level caused by a resonance frequency.
- Continuous diagnostics
Having a continuous data stream that includes both full spectral data and machine speed information enables more precise detection of a machine’s excited states and duration as they occur throughout the day, as well as a better understanding of its forcing functions. Having this information will provide a more accurate assessment of the severity of the resonant vibration. - Simple Bump Test
This method for investigating for a system’s natural frequency involves striking it with a mass and measuring the response. While this type of test can be done with the machine running, it is best to do it when it is not running to more easily identify the equipment’s natural frequencies. A single channel analyzer can be used with either “peak hold” or “triggered” acquisition. It is important to measure the response with multiple averages and locations to get a good idea of where the movement is. Another useful step is to excite/impact the structure at different locations on the structure as well. - Modal Impact test
Whereas a simple Bump Test is used for investigation, Modal Impact Testing is used to confirm the presence of resonance. Testing equipment needs include: at least two-channels of synchronous data acquisition; a Modal Hammer (instrumented with an accelerometer, calibrated in units of force, below a changeable rubber head); at least one response vibration sensor (e.g. accelerometer). Image 1 below shows how resonance data appears while in the field on a data analyzer.
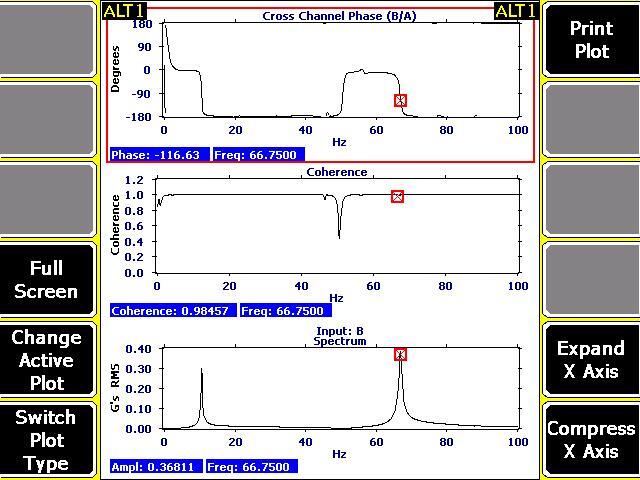
Image 1: Resonance data as seen in the field on a data analyzer
The advantage of this technique is the fact that it enables the monitoring of phase shifts and coherence. The frequency at which the phase shifts 90 degrees with a corresponding increase in vibration is the natural frequency. Modal impact testing provides the ability to create deflection shapes that show the sensitivity (amplification) at various frequencies throughout the structure. Image 2 shown below is the same data as in Image 1 but as viewed on a computer screen.
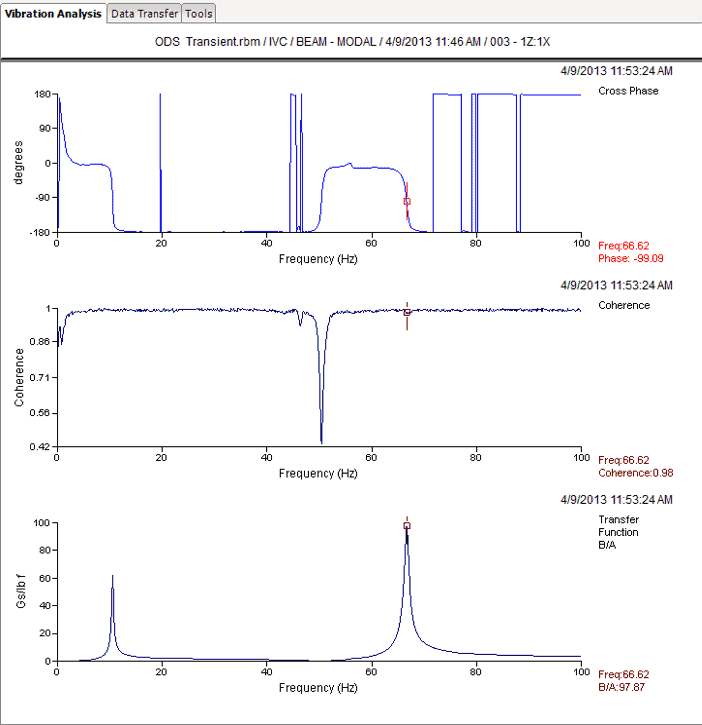
Image 2: Same data as in Image 1 but as viewed on a computer screen
- Run Up Coast Down Analysis
This method utilizes the wealth of information provided from vibration data collected when a machine is either ramping up toward full speed or coming down to rest. As the machine speed changes, shaft vibration (forcing function) will excite natural frequency as it passes through the critical speed. As the machine passes through resonance, the phase will shift 180 degrees, thereby providing proof of resonance.Run-up testing is rarely effective without high-speed data recorders because machinery not on variable frequency drives will start too quickly. Image 3 shown below is an example of resonance data captured from a high-speed data recorder.Image 3: Resonance data captured using a high-speed data recorder
However, more time is usually available when a machine is coasting down to rest. The most common way to perform this test is through the use of a once per revolution tachometer signal fed info a data analyzer which will monitor the vibration and turning speed. Changes in vibration amplitude corresponding with changing phase will enable the location of natural frequencies. Image 4 shown below is an example of coast down data obtained using a once per revolution tachometer.
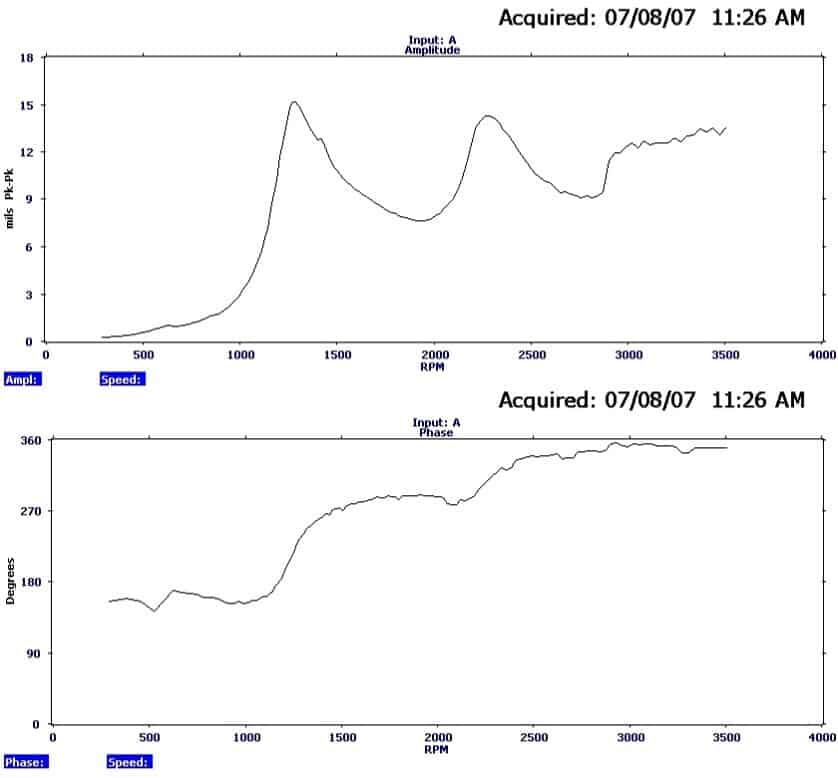
Figure 4: Coast down data obtained using a once per revolution tachometer
Correcting for Resonance
The natural frequency of a structure is dependent upon two main factors: stiffness and mass. As we’ve discussed, resonance occurs when a structure’s natural frequency coincides with any expected forced vibration frequencies (such as unbalance), leading to severe levels of vibration.
Therefore, when a resonance problem has been identified, the goal is to change the natural frequency – either by adding mass to decrease it or increasing stiffness to increase it – so that it is no longer excited by the machine.
While the solution may seem relatively simple, it is actually quite complex, requiring a number of issues that must be taken into consideration. In addition, there are situations in which the natural frequency of a piece of equipment cannot be changed.
At IVC, we have over 30 years of experience with diagnosing resonance issues. If you have equipment that seems to have ongoing issues despite a few “solutions” that only seemed to work for a short time, the problem could be resonance. We can help. Contact us.