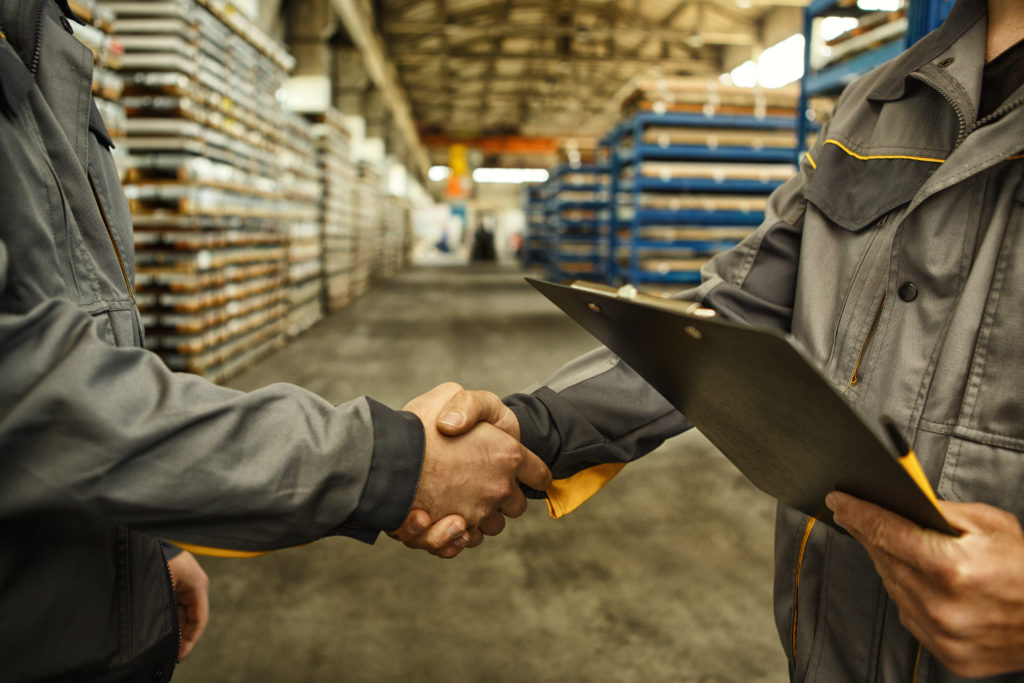
How reliable is your reliability partner?
There are many Condition Based Monitoring (CBM) service providers in business today, each with a slightly different spin on how to achieve the ultimate goal of optimizing machine reliability. Couple this with the ever-increasing number of new, innovative technologies available to conduct them and it’s no wonder people feel overwhelmed.
That’s why it’s extremely important to have a clear understanding of the capabilities and limitations of any outside CBM service providers you are considering to manage your machine reliability program.
At IVC, we’ve had 30+ years of experience with “cleaning up” maintenance messes left by service providers who overpromised during the interview process, explaining all the amazing things they were going to do to keep maintenance costs down, only to underdeliver when the rubber met the road.
So, after hearing similar comments from our current customers about what went wrong with their previous provider, we’ve put together the following five upfront questions every company should ask a potential CBM service provider:
1. What are their core capabilities?
Not all CBM service providers are created equal and it’s important to have a clear understanding of their core capabilities upfront. Here are some things to consider:
- Are they strictly a service company or do they also sell products and equipment?
- What is their core competency? (e.g. Do they specialize in a particular CBM technology, such as vibration analysis, infrared thermography, ultrasonics, etc?)
- If they sell both products and services, are you familiar with the quality and reputation of their products/equipment? If you contract with them, will you maintain the flexibility to purchase whatever products/equipment you may need elsewhere?
- If they are strictly a service company, do they have partnerships with reputable product/equipment vendors?
2. Are they appropriately certified with accredited institutions?
“Certified” and “qualified” do not mean the same thing. Any organization can create an exam and issue a certificate (without there being any evidence that the individual passed the exam.) Accredited training and certification programs contain elements that ensure the process is fair, secure, and meets the needs of the industry. These programs are individually audited to ensure they meet the standards established by the International Standards Organization (ISO).
3. How do they work with customers to ensure a smooth program set up and launch?
To better ensure that your program set up, launch, and ongoing monitoring go as smoothly as possible, an outside CBM provider must have a clear understanding of the following:
- Your company’s maintenance goals and objectives (e.g. specific KPIs)
- How many in-house maintenance team members will be responsible for maintaining the continuity of the program and is it enough?
- What are your most critical assets? It is not realistic to include all machinery in a CBM program. Instead, the focus should be on the assets most critical to the production process. (Ask yourself, “Which of my machines, if it was out of service, would be the most devastating to production?”)
4. What technologies do they deploy and why?
CBM incorporates many different technologies, each one unique in the method with which it identifies machine issues. The most common technologies include:
- Vibration analysis
- Infrared thermography
- Ultrasonics
- Oil Analysis
More advanced testing technologies are also incorporated when the machine issue goes beyond that which the standard CBM technologies can detect and include:
- Modal/ODS testing
- Motion Amplification
- Torque testing
- Transient vibration testing
The more technologies a service provider can offer via appropriately certified analysts, the better. However, the vast majority of CBM service providers only utilize standard technologies and must call in an advanced testing company when a deeper diagnostic dive is required to determine the root cause of a machine issue.
5. What percentage Vibration Route Compliance can they provide and will a monthly route coverage report be provided?
If a service provider promises 100% route compliance, they’re not being truthful.
The reality? 100% route compliance isn’t realistic, and they are just telling you what you want to hear. Additionally, if they deflect by saying: “no one monitors route compliance every month,” you’ll know they don’t plan to stay on top of their inspections and they’re hoping you won’t notice.
What should route compliance be?
Your equipment route compliance should be greater than 80%. Ideally, you should target 85% route compliance. It takes an experienced vibration technician a lot of work and coordination with the operators to get above 80%, but it can be done.
If you have an in-house program, when was the last time you saw your program’s route compliance report? Every reputable vibration unit’s software offers a “canned” vibration route compliance report making tracking incredibly simple.
Choosing a CBM services provider is a big decision, not only due to the monetary investment involved but also, the valuable time spent vetting potential candidates. We hope that the five questions we’ve suggested are at least a good starting point in finding the CBM service provider that is the right fit for your company.
Interested in finding out more about IVC Technologies and our 30+ years as a leading provider in CBM services nationwide? Click here.