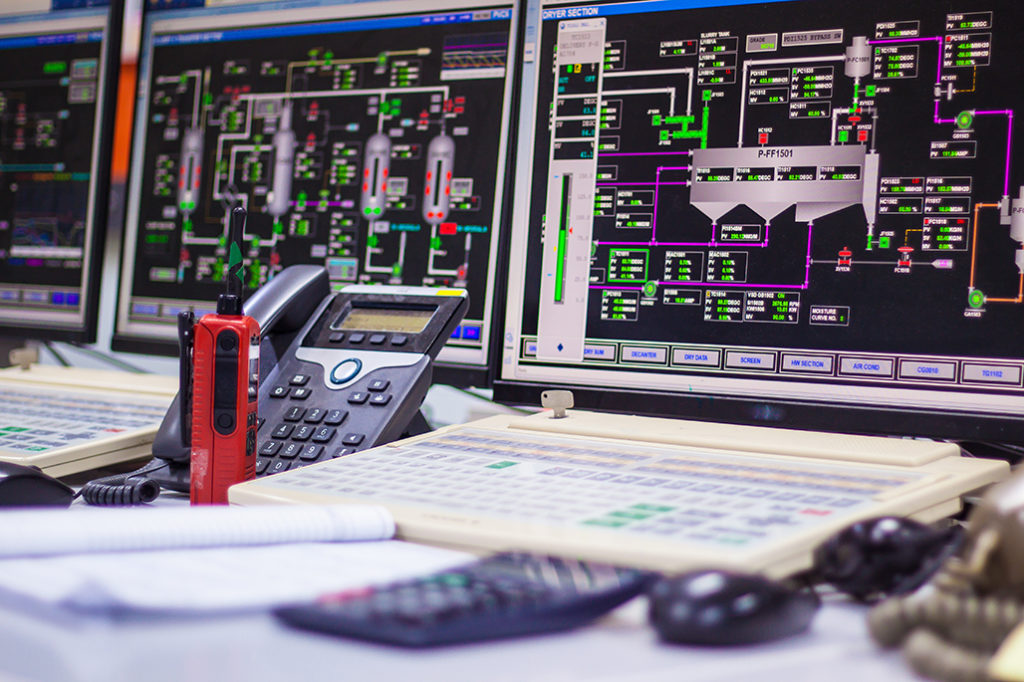
Remote Analysis enables continuous monitoring of machine assets amid limited access to facilities
To say that it’s been a rough start to 2020 would be a huge understatement.
We’ve all been in survival mode – making tough decisions and what we hope are short term adjustments to how we conduct our business, and wondering when life will go back to normal…or if the “normal” we’ve known will ever exist again.
If history has taught us anything it’s that short term measures required during global crises like the one we’re currently facing are often the catalyst for fundamental shifts that affect government policy, industry, and consumer behavior for years to come.
To prepare for the post COVID-19 “new normal”, companies must try to determine which parts of our political, business and social environments will permanently change in the aftermath of the current pandemic and invest accordingly.
Flying blind?
As we’ve unfortunately experienced firsthand, COVID-19 doesn’t discriminate…no business or industry is immune. Manufacturers have been hit especially hard by this crisis and in an unprecedented way with supply, demand, and workforce availability being impacted all at the same time.
In addition, employee safety measures like social distancing and working from home have put additional pressure on manufacturers. While working remotely is a viable option for some, most manufacturing factories are simply not set up to be managed remotely, nor do they have the digital tools and infrastructure required to support such a scenario.
These government restrictions are especially troublesome for companies like ours that provide predictive maintenance service to manufacturing companies. With our access limited to customer facilities, many manufacturers who rely on our services to maintain the health of their critical equipment are “flying blind” and risking catastrophic machine failure and costly downtime.
Unfortunately, for those manufacturers who have resisted getting onboard the Industry 4.0 train, the “new normal” brought about by COVID-19 may leave them little choice if they want to stay competitive.
The good news is, incorporating an online predictive maintenance system doesn’t have to be an overwhelming or bank-breaking endeavor.
A dual approach to predictive maintenance
The methods used for predictive maintenance are always evolving as new innovations designed to make the equipment we use better, faster, and more efficient come on the market.
Historically speaking, IVC analysts have performed vibration analysis on machine assets by going to a client’s facility and physically interacting with critical assets using a portable data collection device. These devices provide the highest amount of resolution into the health of a machine.
However, there are situations when this traditional method of data collection is not possible (i.e. today’s COVID-19 restrictions limiting personnel access) and/or would put the analyst taking data in a hazardous situation. In these situations, remote analysis using smart sensors provides an excellent and safe way to continue monitoring the health of critical assets without having to be onsite.
It’s important to note, that when compared to portable data collection devices, smart sensors operate at a significantly lower bandwidth and a higher noise floor. In addition, the application expertise that licensed analysts bring to the table is extremely tough to displace with smart sensors.
Smart sensors should enhance the human element of a predictive maintenance program, not eliminate it.
That’s why we recommend a dual approach to predictive maintenance. First, use smart sensors and remote analysis to flag a potential machine issue. Then, when an issue is detected, our analyst can schedule a highly efficient and targeted on-site maintenance trip to the customer’s facility to get to the root cause of the problem.
As we continue to face the ramifications of this current crisis, we’re likely to see a rapid increase in the adoption of remote analysis and the technologies that make it possible, as this will be the key to being able to continue offering critical predictive maintenance service during this time of social distancing that could go on for months.
Regrettably, a common misconception surrounding Industry 4.0 is that it is a push for things to shift to being all digital…all the time. This is just not the case. New technological advancements and methodologies play an important role in a multi-faceted, comprehensive approach to keeping manufacturing processes as efficient and malfunction free as possible.
For more information on remote analysis and how best to implement it at your facility, contact us for a free assessment.