More and more companies are harnessing the power of Industry 4.0 and all it entails (IIoT, data, advanced analytics algorithms) and implementing predictive maintenance programs (PdM) in their facilities.
When done correctly and monitored consistently, a PdM program can provide many benefits to a manufacturing facility. A few of these include:
- Reduction in machine failures
- Reduced downtime for repairs
- Reduction in stock of spare parts
- Increased understanding of machine trends
- Increased production
- Increased life of service parts
However, while the benefits of predictive maintenance are numerous, implementing it can be challenging. If done incorrectly, the resulting data produced is likely to be confusing for the untrained and probably inaccurate, therefore diminishing its value and the overall effectiveness of the PdM plan.
The following are five tips that we recommend to our customers to better ensure a successful implementation and sustainable PdM strategy:
1. Have a plan and start small
As is the case when starting any major project, it’s imperative to have a well-defined plan that clearly defines the desired business outcome and project scope.
It’s easy to get caught up in all the “tech hype” of Industry 4.0 and invest in more than you need or sometimes things you really don’t understand or need at all. That’s why we advise starting small, assessing and adjusting as you go, and then using the data and insights gained for purposeful, efficient expansion.
2. Identify critical assets
Not every asset needs to be included in your PdM plan – it just isn’t cost-effective. Instead, your PdM plan should be reserved for those assets that are the most critical to your business process.
Generally speaking, a critical asset is one that:
- Has high repair/replacement costs and a record of frequent breakdown incidents
- Has a long lead time for spare parts and/or direct replacement
- Causes significant disruption or a complete shutdown to production when a breakdown occurs
- Poses a hazard/safety risk to the work environment and/or personnel when not operating at optimum efficiency
- Requires the attention of a specialist to get it back online due to its complexity
- Demands significant financial resources and personnel
Assets that meet the above criteria are the best candidates for your PdM program.
3. Obtain actionable data
Machine records are an invaluable and time-saving source for acquiring actionable insights on selected equipment. Sources for historical data include hard copy maintenance records and charts, CMMS, enterprise software from other departments, and input from maintenance technicians and machine operators who work with the machines on a daily basis.
4. Identify failure modes
Condition based monitoring operates on the assumption that all machines will deteriorate and fail partially or fully at some point and is a key component in identifying an asset’s failure modes (i.e. the different events or ways in which an asset can fail.)
While the asset is running, strategically placed sensors are able to detect changes in the machine’s condition that may lead to failure. Identifying failure modes will help in choosing the appropriate condition monitoring technique.
For example, vibration analysis is the most commonly used technique for rotating equipment because of its ability to detect faults common to this type of equipment, such as gear wear, shaft misalignment, unbalance, bearing wear and mechanical looseness.
PdM tools commonly used include but are not limited to: accelerometers, tachometers, thermal cameras, and even advanced acoustic/ultrasonic imagers like the Fluke ii900 Sonic Industrial Imager.
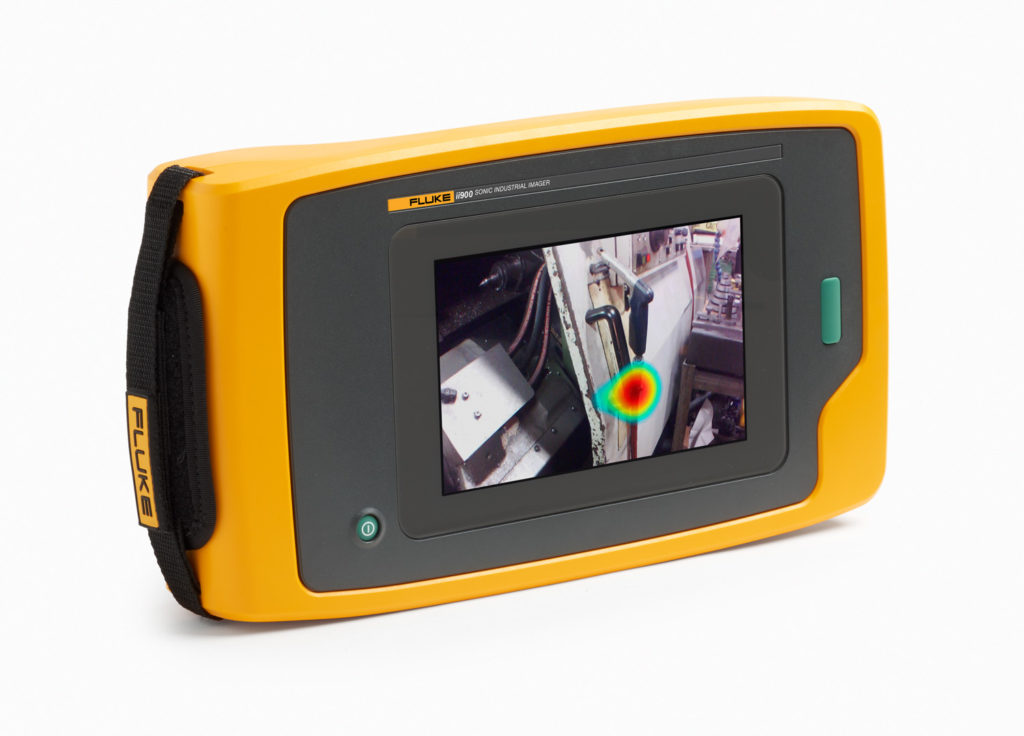
Fluke ii900 Sonic Industrial Imager
5. Scale the approach to fit what the Asset needs
Not all assets are created equal so just as there are varying levels of criticality, there are also varying levels of coverage.
Levels of coverage include:
- No coverage because it’s a non-critical low cost spared asset
- Periodic PdM program checks that are well within the timeframe of the identified failure modes
- Online surveillance monitoring on assets that have a higher criticality and/or have failure modes that can’t be addressed through periodic monitoring including IIot
- Online continuous monitoring and advanced analytics for the most critical assets which require 24/7 monitoring, alarming, and in some cases protective shutdown capability
Good programs utilize a mix of these approaches and more based on their specific monitoring needs, budget constraints as well as company culture. Therefore, the best solution is also going to be one that is tailored to fit your specific situation and needs – not a shoehorned solution that someone else paid for, wrapped in a pretty presentation that will typically start off with “All you have to do is just…”.
Being able to avoid a potentially catastrophic failure using predictive tools on a key piece of equipment is a game-changer for manufacturers in the ultra-competitive market in which we currently find ourselves.
If you’re serious about implementing a PdM program at your facility, contact us – we are here to help you.