As discussed in last month’s blog, it’s extremely important for anyone involved in vibration analysis to understand the basics of phase or simply put, how things are moving relative to each other. The next step in the journey is learning how to take this basic understanding of phase and apply it in order to solve problems that every vibration analyst will surely encounter.
One important aspect of being able to do this successfully is knowing and understanding some of the primary tools available. When it comes to phase analysis, a wide variety of tools and methods exist, ranging from very simple to quite complex, depending on the nature of the problem. Here are a few common machine problems easily identified by phase analysis:
Soft Foot
Soft Foot is present when not all of a machine’s feet sit flat on the supporting base, resulting in distortion of the machine case when the mounting bolts are tightened. The distortion can be confirmed by observing dial indicator movement on the mounting foot while loosening its mounting bolt.
Other conditions that affect the feet are inadequate bolt tension, sprung foot and squishy foot (i.e. too many shims). These are very common problems encountered in the field and simple phase checks are a perfect way to accurately identify the condition. As you can see in Figure 1, when the foot is properly fastened to the base, vibration phase measurements taken on both the foot and the base will be “in phase” with each other and moving in unison.

Figure 1: Properly Mounted Foot – In Phase
In comparison, the soft foot condition represented in Figure 2, indicates that the foot and base do not move in unison because the two are not properly fastened together. This results in them moving “out of phase” with each other. Thankfully, this is another situation that can easily be identified with simple phase measurement, while the machine is operating.
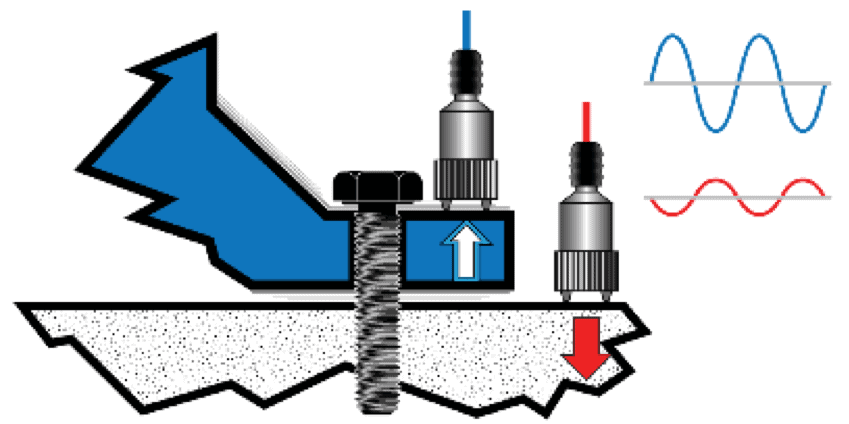
Figure 2: Soft Foot – Out of Phase
Misalignment
Another common issue that vibration analysts often encounter is misalignment – particularly across couplings. Again, phase analysis is the “go-to” tool to quickly and accurately identify the nature and severity of the misalignment. If the alignment is correct across the coupling, both the phase and amplitudes should be essentially the same and within acceptable limits, as shown in Figure 3.
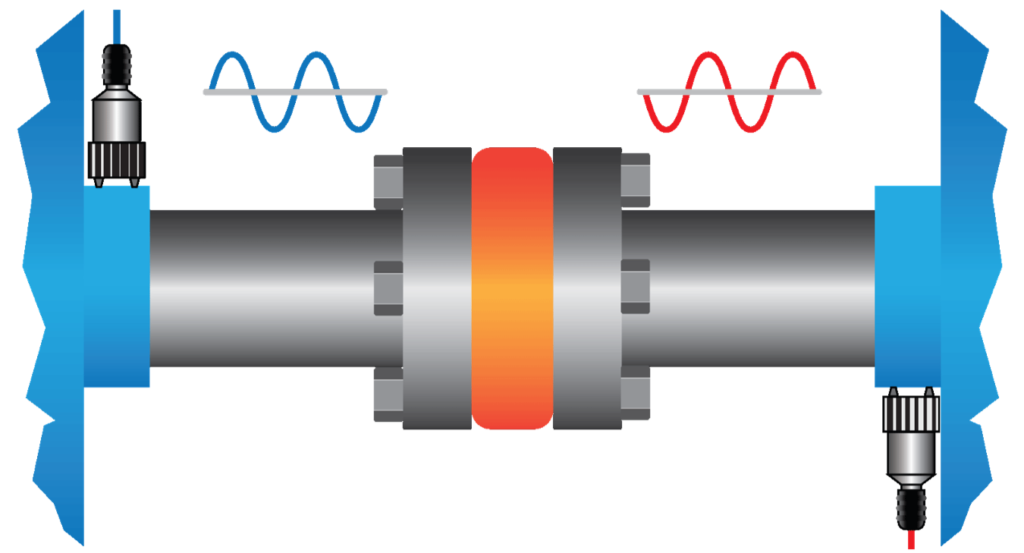
Figure 3: Properly Aligned Coupling – In Phase
Conversely, if there is an offset misalignment across the coupling as shown in Figure 4, then there will be a significant phase shift in the radial directions. This too can quickly and easily be identified using phase analysis.
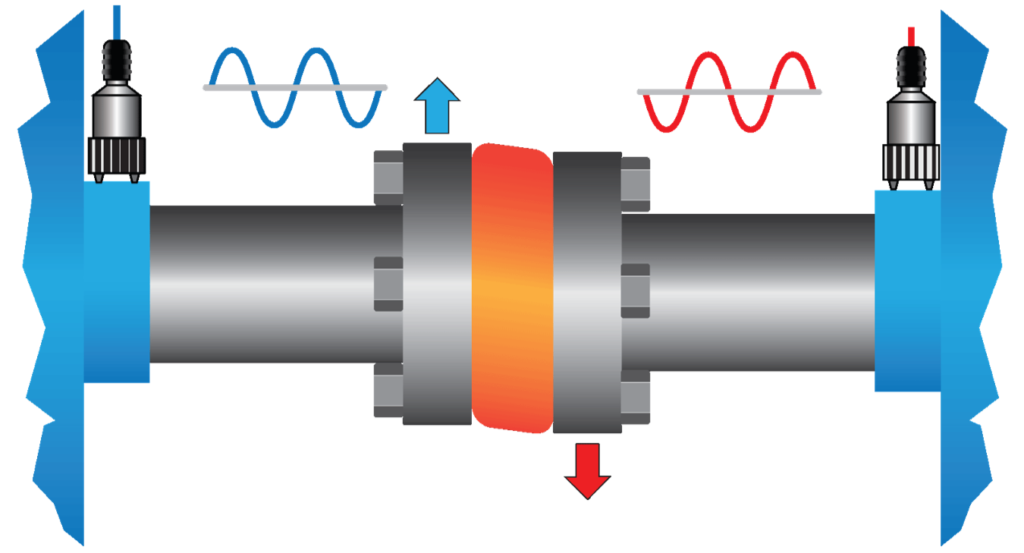
Figure 4: Offset Misaligned Coupling – Out of Phase
In the case of angular misalignment shown in Figure 5, instead of the phase shift being in the radial direction, it will show up in the axial direction. This type of misalignment is of particular concern because there can be large and very detrimental thrust forces generated. The coupling will typically be rated to handle the misalignment and associated forces but that is not normally the case for the bearing on either adjacent side of the coupling.
Again, basic phase analysis is the “go-to” process to identify this malady. In this scenario, it is important to remember that you will usually induce a 180-degree phase shift (because of sensor orientation as shown below) which has to be accounted for.
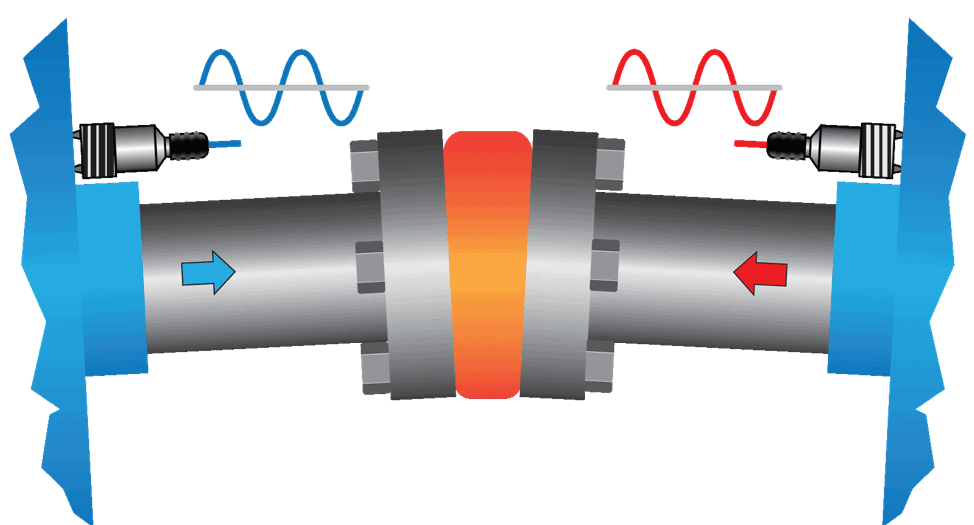
Figure 5: Angular Misaligned Coupling – Out of Phase
A Picture is Worth a Thousand Words
If the complexity of a machine problem requires a more in-depth phase analysis, there are more advanced tools such as Modal Analysis, Operating Deflection Shape (ODS) Analysis, and even Motion Amplification™️ that can be used to identify and solve the problem. Although these methods are more complex and involved, the resulting data is usually in the form of a picture as shown in Figure 6, helping analysts to easily visualize and better understand the root cause and determine the right fix for even the most difficult structural and mechanical problems.
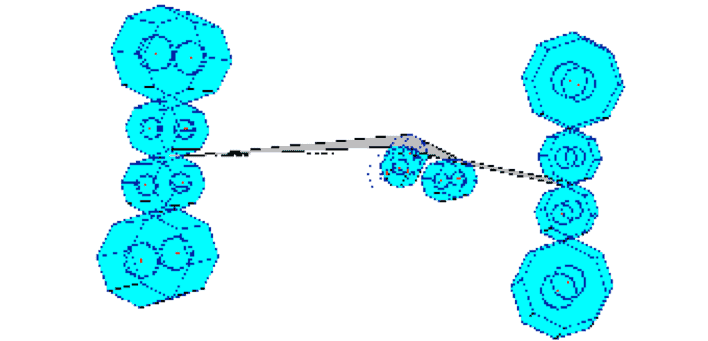
Figure 6: Inter-stand Roll Dynamic Misalignment ODS
Regardless of which method is necessary, IVC Technologies has the personnel and technical capabilities to get your problem resolved. For more information, click here.