As any analyst can attest, vibration analysis isn’t a cut and dry, cookie-cutter process for a myriad of reasons, such as the fact that:
- Machines typically have more than one vibration-inducing fault
- Many fault types have similar frequency patterns
- Some vibration measured is the result/effect of other problems in the machine
Sometimes, a deeper dive is required to get to the root cause of machine vibration issues. One of the most powerful, but too often neglected diagnostic tools available to do just that is phase analysis.
What is Phase?
Phase is the relationship between two signals of the same frequency, measured in degrees. A phase study is simply a collection of phase measurements made on a machine that is evaluated to reveal information about relative motion between measurement points. Phase is independent of amplitude. That is to say that each signal may have different amplitudes and still be evaluated for specific phase characteristics.
In Figure 1, the sine waves (vibrations) of Machines A and B do not reach their positive peaks at the same time (i.e., when Machine A reaches the top of the peak, Machine B is at the bottom). This is an indication that they are “out of phase.”
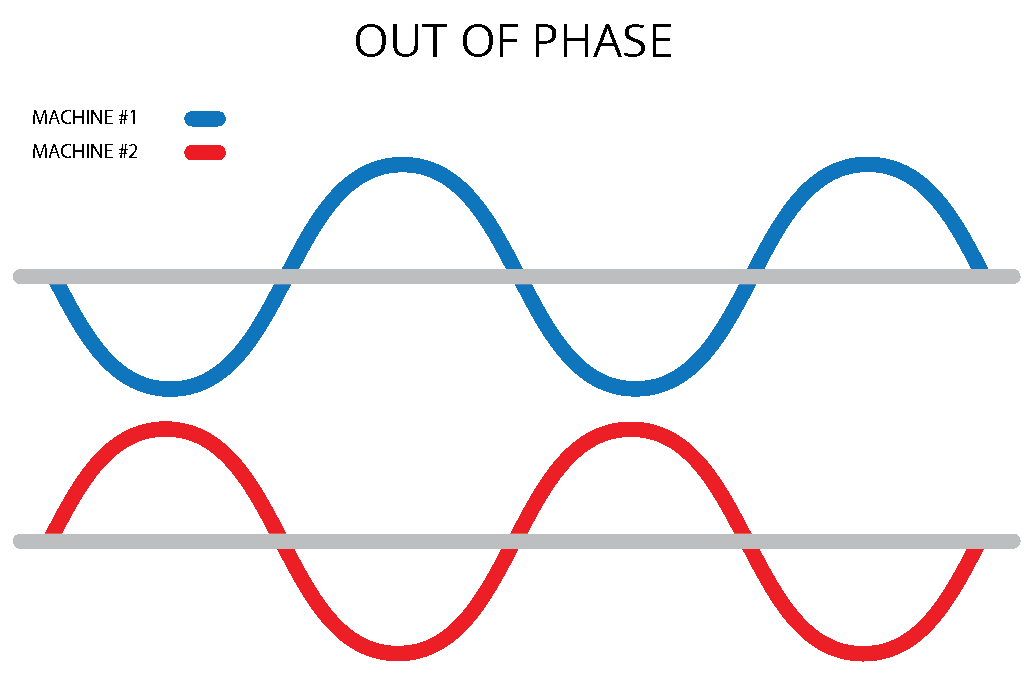
Figure 1: Out of Phase
In Figure 2, the sine waves (vibrations) of Machines A and B reach their positive peaks at the same time – an indication that they are “in phase.”
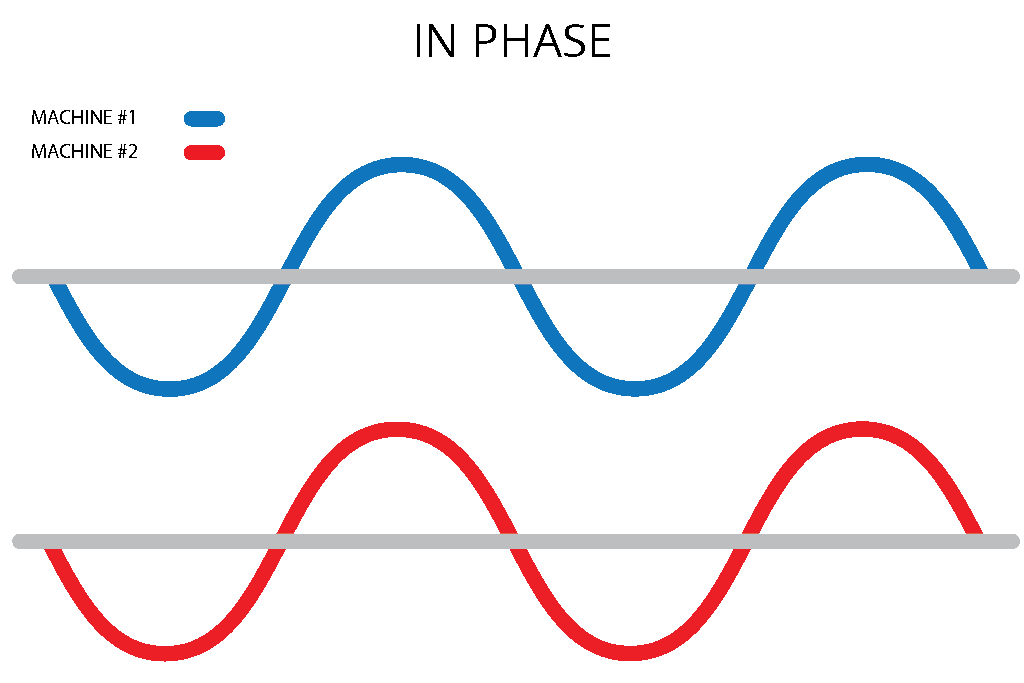
Figure 2: In Phase
Absolute vs Relative Phase
In vibration analysis, phase can be measured using either an absolute or relative reference. Most single channel vibration analyzers can measure absolute phase of a signal, relative to an absolute reference such as a tachometer pulse. It is measured at shaft rotational frequency or any integer multiple of shaft speed (i.e., synchronous frequencies). Basically, the analyzer calculates the time between the tachometer trigger and the next positive waveform peak vibration at each measurement point. The time interval is then converted to degrees and displayed as the absolute phase (Figure 3). Absolute phase is required for rotor balancing.
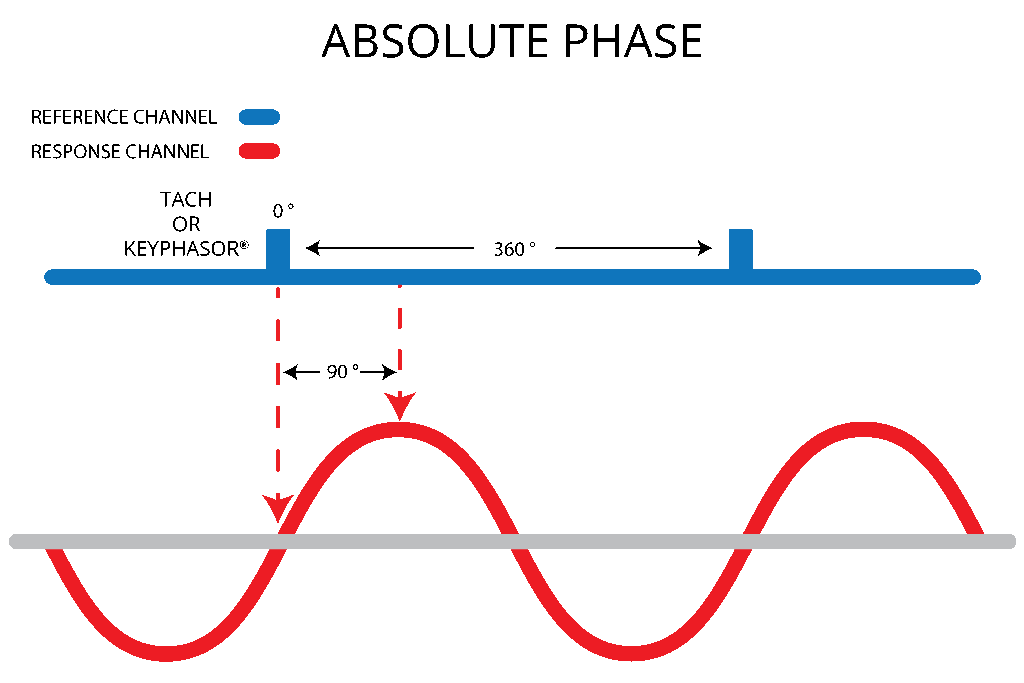
Figure 3: Absolute Phase
Relative phase uses two measurement points. The first channel is designated as the reference point and the second channel as the response point. The relative phase difference is measured between the two.
The analyst may choose any two points to apply two sensors (of the same type). Relative phase is the time difference between the maximum peak of each waveform at a specific frequency, converted to degrees (Figure 4). Relative phase does not require a tachometer so phase can be measured at any frequency. Often times, absolute phase is not necessary because many diagnoses, such as identifying loose foot or soft foot, are made by analyzing relative phase.
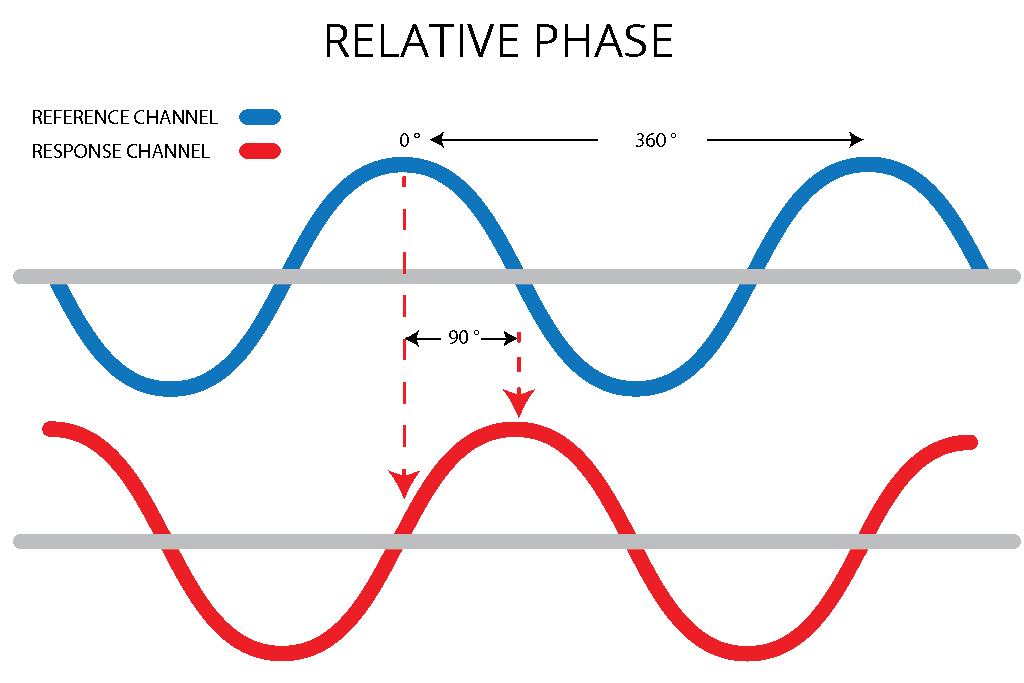
Figure 4: Relative Phase
Cross channel phase is a measurement of relative phase. It requires a two-channel analyzer/data collector such as the VIBXPERT II from PRUFTECHNIK that can record cross channel phase as route data (not all two-channel data collectors have that capability. Shown in Figure 5.)
For measuring cross channel phase, one single-axis sensor serves as the fixed reference and is placed somewhere on the machine – usually on a bearing housing. The response sensor may be a single-axis or triaxial sensor which is placed at a second location. If a multitude of phase measurements are going to be made, such as when building Operating Deflection Shape (ODS), the response sensor is moved sequentially to all of the other test points.
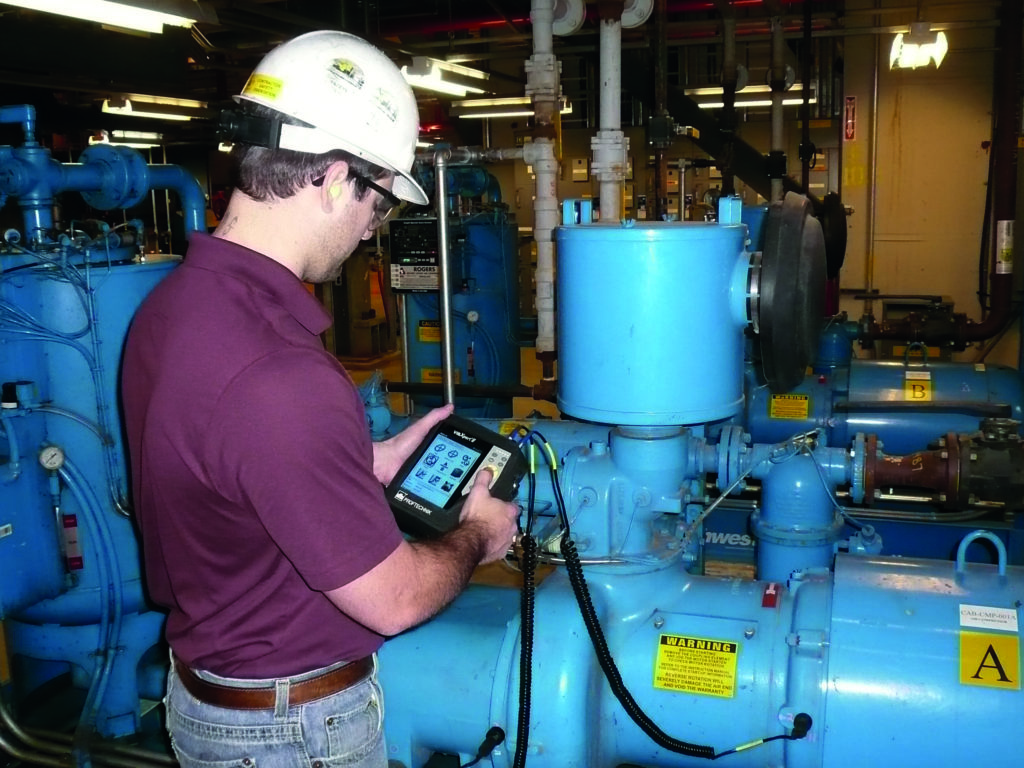
Figure 5: VIBXPERT II from PRÜFTECHNIK in use
At each test point, the analyzer compares the two signals from the fixed and roving sensors.
Problems such as misalignment, looseness and bent rotor are more easily diagnosed when cross channel phase data is included with amplitude and frequency measurements.
When to use Phase Analysis
Phase analysis should be used on machine problems when the source of the vibration is not clear or when it is necessary to confirm suspected sources of vibration. A phase study might include points measured only on the machine bearings or can include points over the entire machine from the foundation up to the bearings.
Situations in which phase can significantly help with analyzing vibration include looseness/bending/twisting, misalignment, soft foot, bent shafts and rotors, cocked bearings, resonance, and imbalance.
Conclusion
Amplitude, frequency and phase information are critical components for any reliability-based maintenance program. A lack of phase information can not only inhibit an analyst’s ability to diagnose a machine problem, but it can also result in an incorrect diagnosis.
Understanding phase and how to interpret it is a huge step to becoming a better analyst. In next month’s blog, we’ll tackle the specifics of how to use phase analysis to identify the aforementioned machine problems.
For information on having an IVC analyst conduct phase analysis on your machinery, click here.