Routine condition-based monitoring (CBM) is a must for maintaining the operation and reliability of rotating equipment in factories and power plants. While most CBM programs include – among other things – cleaning, lubrication and oil checks, many neglect to include shaft alignment into their plan. Instead, they perform it only when something fails. However, studies reveal an alarming statistic…
Over 50 percent of all machine damage is caused by incorrect shaft alignment
Therefore, why not incorporate shaft alignment into your routine CBM plan? A precision laser alignment check takes very little time to execute and could uncover a potential problem that might end up costing your company hundreds of thousands of dollars in unscheduled downtime and equipment repairs.
Every millimeter matters – that’s why laser alignment is key
Thermal imaging of inaccurately aligned pumps shows how couplings, roller bearings, and seals can get extremely hot. Misalignment, even by a few tenths of a millimeter, leads to machine overload. In turn, overloading a machine can result in coupling damage, seal wear, bearing damage or machine vibrations that significantly reduce the service life of the various components. Consequently, misalignment can also increase energy consumption and in the worst case, cause expensive production losses.
Mechanical measuring methods align the surface of two couplings only. If these surfaces have a layer of paint or rust on them, correct alignment is no longer possible. In contrast, laser alignment determines the actual rotational axis by rotating the shafts so surface quality doesn’t influence the results.
If the measuring arms sag one-tenth of a millimeter, measuring with a precision to the hundredth doesn’t make sense. As a result, rounding and readout errors accumulate quickly.
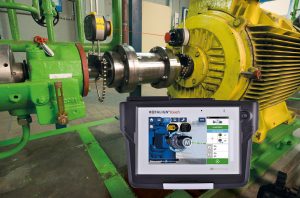
ROTALIGN laser alignment system
3 quick steps to alignment
At IVC, we pride ourselves on utilizing the best cutting-edge technology on the market to provide the most efficient, comprehensive vibration and dynamic analysis for our clients. Using the ROTALIGN laser alignment system from Pruftechnik, our analysts can complete a measurement for our clients in three quick steps:
- Enter dimensions
- Rotate shafts
- Readout results
Done.
With this system, we are able to complete shaft alignment covering a wide range of applications. These include simple coupling systems, frequent pumps and motors, and complex systems with multi-stage turbines and compressors.
The cost of replacing components can amount to over half of the procurement costs of a pump. The replacement of seals, bearings, couplings, and shaft, the additional power consumption and expensive production losses accompanying poor shaft alignment can quickly leave a big hole in the operating company’s pockets. Routine CBM can go a long way in preventing those holes from happening.
Contact us for a CBM plan tailored specifically to your company’s needs.