This is Part 4 in our 4-part series on maintenance programs and benchmarking. If you missed Part 1, Part 2 or Part 3, read them now. In the final installment, we discuss how much value preventive maintenance (PM) actually delivers.
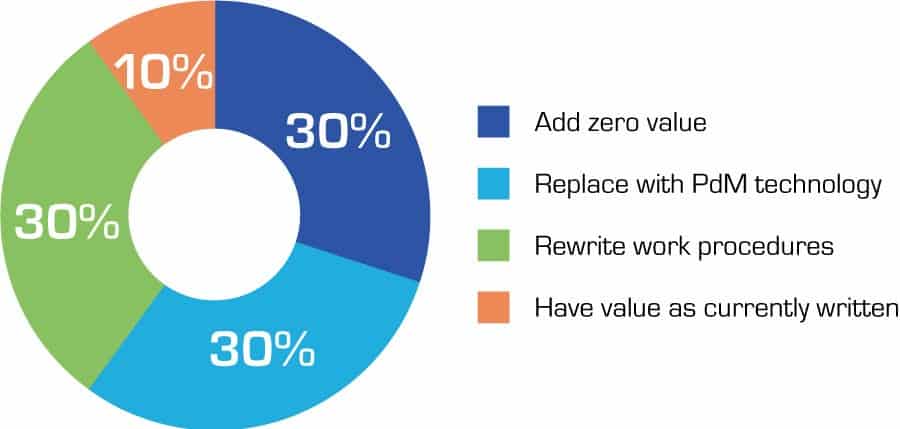
Source: The Federal Energy Management Program’s Operations & Maintenance (O&M) Best Practices Guide.
According to The Federal Energy Management Program’s Operations and Maintenance (O&M) Best Practices Guide, 31 percent of organizations in the United States use preventive maintenance (interchangeable spelling preventative maintenance) as their predominant mode of maintenance. Unfortunately, O&M also concludes there’s a lot of room for improvement here. In observation of the 30/30/30/10 Rule for Preventive Maintenance, you’ll find that:
- 30 percent of PMs being performed today add zero value
- 30 percent of PMs performed could be replaced by a predictive (PdM) technology (Vibe, IR, OA, UE, NDT).
That means 60 percent of preventive maintenance programs are a complete waste of manpower
- Then, 30 percent of PMs could add value if work procedures were rewritten to include enough description to specifically target and eliminate failure modes.
- As a result, this leaves only 10 percent of PMs with any value whatsoever as they are currently written.
Top performers have a higher percentage of their equipment on non-intrusive, predictive technologies
The table below indicates the value in implementing a more predictive maintenance (PdM) plan as a means of increasing asset longevity, reducing maintenance costs and unnecessary inventory, and significantly decreasing a company’s overall downtime.
Figure 1: Benchmarking for Power Generation*
Download full Benchmarking Data Report*
The final column in the table above indicates the percentage of equipment on bill of materials (BOM), which simply means that “like” equipment types are linked within the CMMS system. Linking “like” equipment in the CMMS is the simplest way to draw on storeroom inventory while ensuring coverage with the number of parts on hand.
Gaining information through measurement, especially proper measurement, can provide valuable data required to achieve any benchmark/goal for continuous improvement. In conclusion, the benefits of predictive programs far outweigh those of preventive programs. In addition, benchmarking offers insights into how top performers achieve those results, and how you can become a top performer.
Learn more about the solutions for equipment maintenance offered by IVC Technologies, including Condition Based Monitoring (CBM), Advanced Testing, and Training for optimal asset health, reliability, energy savings, cost savings, productivity, safety, and profitability.
*All RAV industry table information provided courtesy of Management Resources Group, Inc., an Emerson company. © Emerson. All Rights Reserved