This summer IVC attended and presented to over 200 maintenance professionals at the AIST Crane Symposium. The most common problems of industries affected by overhead crane failures were the emergency egress when they break down, and the limited access for crane preventive maintenance and routine inspections. You see, whenever overhead cranes breakdown, they’re never where the operator can just get off, or maintenance can go up to work on them. Somehow, cranes always break down in the worst spot of the track.
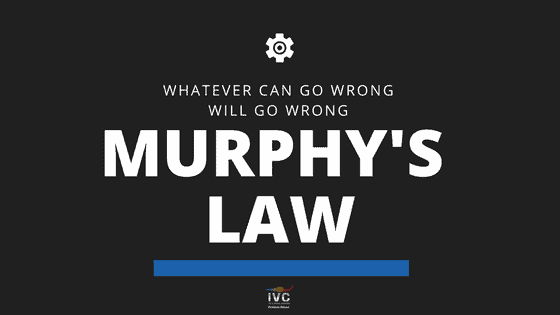
When overhead cranes break down, it’s always in the worst spot of the track, never where the operator can get off or maintenance can work on it.
Overhead Cranes Are Complex
Overhead cranes are more complicated to maintain and inspect than many other equipment types. There are OSHA regulations in place that purposefully limit access due to the inherent safety risk involved within industrial environments as you move large, heavy loads overhead across the bridge spanning a gap. In most cases, you will not be able to access or perform vibration testing of the crane while it’s loaded and in operation. When you can only inspect your crane when it’s in maintenance mode and not while it’s loaded and operating, that diminishes the quality of the data you can gather.
Obstacles to Increasing Inspections on Cranes
Safety requires observance and adherence to guidelines and procedures established by governmental agencies for good reason. Limited crane access can be further complicated by the additional PPE requirements such as harnesses to protect against falls when attempting to access crane equipment. For these reasons, additional inspections are ignored in favor of only the OSHA annual inspection requirements because to do anything additional would be a huge hassle in so many other ways.
When it’s time to go up and do an OSHA regulated inspection, such as a visual wire rope inspection, you’ll probably do more than that. You may check the oil levels and visually inspect a couple of other things. Though both of these preventive (PM), time-based maintenance tasks are important, neither will tell you if a bearing is going to fail or gears are wearing out. You will want to apply additional condition monitoring and advanced vibration testing to improve the uptime of your cranes which results in productivity improvements. Crane and hoist safety and operational defects are significantly reduced, and equipment reliability is improved following the development and implementation of advanced vibration inspections, diagnostics, and analysis.
For more on advanced vibration technology applications for overhead cranes, check out our resources page.
jresquival says
That’s a good tip to inspect other things when doing the OSHA mandated inspection. That way you’ll efficiently check on the operation of the whole crane. If you do proper maintenance and inspections on your equipment it will last longer and save you money.